Economical right from the start
In order to guarantee an economical operation of a boiker system, we place particular value on a continuous, trouble-free fuel transportation system. This requires, that the fuel discharge, fuel transportation and fuel feed optimally coordinated.
LAMBION provides different systems for all combustible residues and waste components.
Fuel Discharge
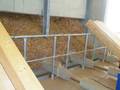
Push Floor Systems
Application: for rectangular and square supply equipment, silos with a discharge lengths of to 14 m (46')
Material to be conveyed: uncut/uncrushed material, edge length max. 0.5 m (1,8")
Output Range: up to 20 m3/hr. (706 ft3)
Technology: Depending onthe size of the supply equipment the LAMBION-push floor consists of two or more push floor rods incl. carrier. The number of push floor rods is not limited and depends on the width of the storage area. The push rod itselfs is made of a carrier profile on which the thrusting wedges are arranged at specified intervals across the thrust direction. A hydraulic lifting cylinder is mounted to the end of the support rail, moving the push rod back and forth. During the forward motion the thrusting wedges brace against the discharge material and push it through the discharge port.
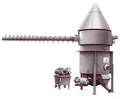
Rotary Spiral Auger Discharge System
Application: for round supply equipment with a diameter of 4 to 12 m (13 to 39')
Material to be conveyed: cut/crushed material
Output Range: up to 40 m3/hr. (1,400 ft3)
Technology: The machine consists of a 360 degrees rotatable discharge head with drive, pivoted in the centre of the silo floor. The discharge screw is mounted with single sided bearings inside the discharge head, the fuel is carried to the centre of the discharge head and down from there. The combination of screw auger rotation with the simultaneous rotation of the discharge head allows for a continuous, well controllable discharge from round silos, and safely avoids fuel bridging in the silo.
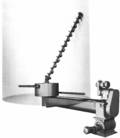
Leaf Spring Auger Discharge System
Application: Round silos with a diameter of up to 5 m (16' 5") and a height of 10 m (32'm 9")
Material to be conveyed: light cut/crushed fuels with a particle size of 50 mm (2")
Output Range: up to 5 m3/hr. (177 ft3)
Technology: The machine consists of a screw auger, which is securely mounted inside the silo, an agitator with flat spring arms and an attached loosening screw is installed at the end of the auger inside the silo. The discharge screw is operated by a continuously speed adjustable motor, enabling adaptability to fluctuating fuel structures. Due to its simple structure and for smaller system scales, it is an economically interesting alternative to a Rotary Spiral Auger Discharge System.
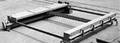
Moving Auger Discharge System
Application: for rectangular and square supply equipment with a discharge lengths of up to 5 m (16' 5") and a discharge width of up to 8 m (26' 3")
Material to be conveyed: uncut/uncrushed material, edge length max. 0.3 m (1')
Output Range: up to 10 m3/hr (354 ft3)
Technology: Two screw spirals are arranged parallel to each other across the discharge system and are hydraulically moved in a reciprocating motion over the entire silo area. The combination of the screw turning simultaneously to the lateral movement allos for a continuous, well controllable discharge from rectangular storage spaces and at the same time avoids fuel bridging in the silo.
Fuel Transport
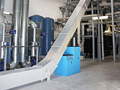
Drag Chain Conveyor
Material to be conveyed: Wood Chips, Shavings, Dust, Pellets, Shells, Bark, Pulses, Kernels, Coal, edge length up to 300 mm (12")
Transport Distance: up to 35 m (330')
Output Range: up to 10 t/h
Technology: Handling of large height differences and long conveying paths between silo and furnace feed-in through. Available in primary or secondary layout, as well as upper face or lower face conveyor, depending on the structure of the transported material.
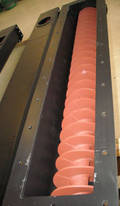
Screw Conveyor
Material to be conveyed: Wood chips, Shavings, Dust and Bark
Transport Distance: up to 8 m (26')
Output Range: up to 8 t/hr
Technology: Trough screw conveyor and pipe screw conveyor in solid design with bearings fixed on both sides of the screw spiral. Embodiment in painted steel, alterntively in stainless steel.
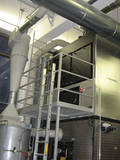
Pneumatic Conveyor
Material to be conveyed: dry to moist shavings and wood chips, edge length up to 50 mmm (2")
Transport Distance: up to 100 m (330')
Output Ranfe: up to 4 t/hr.
Technology: The fuel is fed through a pipeline by carrier air. LAMBION plans and delivers the complete installation incl. fans, pipes, locks, filters and separators.
Fuel Feed
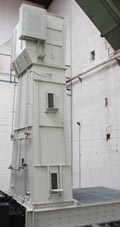
Hydraulic Fuel In-Feed
Material to be conveyed: Coarse fuels, edge length up to 600 mm (24”)
Transport Distance: up to 3 m (118’)
Transport Width: up to 2.4 m (7’ 10”), matching the width of the furnace
Output Range: up to 10 t/h
Technology: The fuel is being conveyed through a rectangular, horizontally placed shaft. A robust rectangular feed piston, driven by two parallel -connected hydraulic cylinders, is moving the fuel. The front edge of the piston is equipped with a cutting blade made from hardened steel, which is cutting off over sizes in the fuel. Included are dosing container with level control, level monitoring and extinguishing equipment and optional the hydraulic unit. The dosing container is placed directly on the feeder and built conically rectangular.
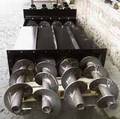
Multiple Screw Feeder
Material to be conveyed: Fine and coarse fuels, edge length up to 300 mm (12”)
Transport Distance: up to 4 m (158’)
Transport Width: up to 2.4 m (7’ 10”), matching the width of the furnace
Output Range: up to 10 t/h
Technology: The fuel is being conveyed through a rectangular, horizontally placed shaft. Two to six screw spirals with a diameter of 280 mm (depending on the version) are arranged in parallel inside the shaft. This layout enables the continuous and very well controllable transport of both coarse and fine fuel particles, while simultaneously being unsusceptible to over-sizes. Included are dosing container with level control, level monitoring and extinguishing equipment. The dosing container is placed directly on the feeder and built conically rectangular.
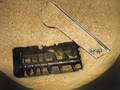
Stoker Feeder
Material to be conveyed: dust, shavings, wood chips, shells and pellets
Transport Distance: up to 3 m (49’)
Transport Width: up to 2.4 m (7’ 10”), matching the width of the furnace
Output Range: up to 4 t/h
Technology: Heavy drag chain conveyors (upper face), to transport coarse, uncut/uncrushed fuels. Including fuel feeding unit with hydraulically operated valves and level monitoring for the direct feed of grate firing systems.
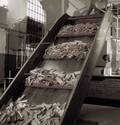
Wood Log Feeder
Application: as feed-in system for grate furnaces utilizing primarily uncut/uncrushed materials
Material to be conveyed: uncut/uncrushed material, edge length up to 1 m (3’ 3”)
Transport Distance: up to 15 m (49’)
Transport Width: up to 2.4 m (7’ 10”), matching the width of the furnace
Output Range: up to 4 t/h
Technology: Heavy drag chain conveyors (upper face), to transport coarse, uncut/uncrushed fuels. Including fuel feeding unit with hydraulically operated valves and level monitoring for the direct feed of grate firing systems.
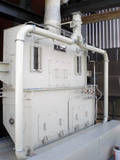
Dosing Rotor Feeder / Flap Roll
Material to be conveyed: Flow able fuels, edge length up to 50 mm (2”)
Transport Distance: Installation directly above the furnace
Transport Width: up to 2.4 m (7’ 10”), matching the width of the furnace
Output Range: up to 4 t/h
Technology: Designed as a rotary valve in full metal construction, the conveyor width corresponds to the width of the furnace. The drive is continuously adjustable by means of a geared motor with frequency converter, which allows an absolutely uniform and well-controlled fuel metering. Including dosing with level control, monitoring and extinguishing equipment. The dosing container is placed directly on the feeder and conically rectangular.
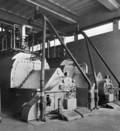
Injection System
Material to be conveyed: Dry, dusty shavings and wood chips, edge length up to 50 mm (2”)
Transport Distance: up to 200 m (656’)
Output Range: up to 3 t/h
Technology: Direct transport of the fuel from the silo to the furnace by means of a transport-fan or indirect transport by rotary blowers, each including fan, pipes, locks, and the injection nozzle for installation in the furnace, in stainless steel or cast iron construction. The systems are well suited for retrofitting existing furnaces and boilers of all brands.
LAMBION Fuel Feeding Systems
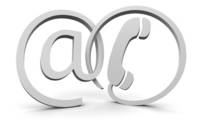
Are you interested in our Fuel Feeding Systems or have you any questions?
Then contact us:
Phone +49 5691 807-0
Fax +49 5691 807-138
office[at]lambion.de